機能安全における製品認証のコツ
製品認証
本稿ではプロジェクトマネージャ向けに機能安全認証取得に向け、具体的になにをすべきかにポイントを絞って触れる。
機能安全認証のポイントは、一言で言えば「安全システムの設計」である。すなわち安全機能とそのアーキテクチャおよび診断機能を決定し、適⽤範囲を明確にすることである。これが出来ていない為に必要以上の事を行ったり、必要な事が抜けていて進まなかったりして、認証開発が長期化し開発工数も無駄に多くなるという悪循環に陥ってしまうので、しっかりとした検討およびシステム設計を行って頂きたいところである。
(※) 下記URLよりダウンロード可能 https://wp.techfactory.itmedia.co.jp/contents/37949
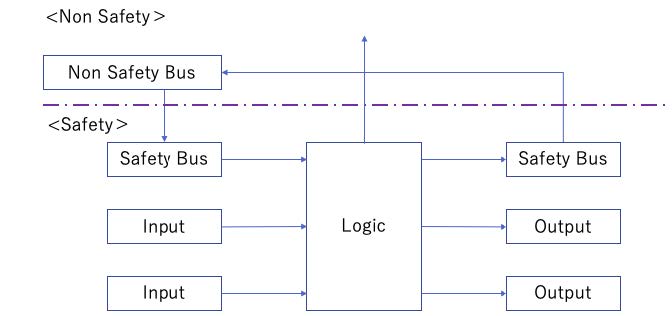
安全システムの設計とは、まず安全機能の入力(Input)と処理(Logic)と出力(Output)を意識しながらシステムブロック図を書くことである。次に、これらを分析し方策(診断機能)を追加して故障が発生しても必要な安全性が確保できるシステムにする。
これにより、妥当性のある安全システムとその適用範囲を明確にすることができる。
この後の実開発においては、製品認証では安全度に応じた信頼性の担保された製品設計を要求しており、製品開発で使用される各種技術は、それらに対応する必要がある。つまりソフトウェア技術・ソフトウェア開発支援ツール・シリアル通信技術なども信頼性の担保された設計が必要となるのである。
車載/非車載品における差と今後のトレンド
機能安全認証を語るとき、車載分野と非車載分野では対応が異なることをご存じだろうか?
例えば、車載ではSW/HWの構成や開発手法はどの製品でも似ており、対象規格もISO 26262が中心となるため、ノウハウが共有しやすい。例えば、車載ではSW/HWの構成や開発手法はどの製品でも似ており、対象規格もISO 26262が中心となるため、ノウハウが共有しやすい。
一方、非車載分野ではSW/HW構成や開発手法は多種多様で、IEC 61508を参照しながら個々の製品規格対応が必要となるため、有用なノウハウがメーカ内から出ることは先ず無い。
IEC 61508では第三者認証が必須であるが、ISO 26262ではOEM(自動車メーカ)の自己認証と事実上なっている点も大きな違いだ。
これらの違いを踏まえると非車載分野の認証の方が難しくみえるが、産業分野での第三者認証は10年以上前から実施されており評価方法が確立されている為、実際にはどの様な製品でも対応可能である。
最新のトレンドでは、セットメーカがシステム認証を取得するだけなく、部品メーカがコンポーネント認証を取得する例も増えており、今後も認証済みコンポーネントの活用が進むと予想される。
自社でやるべき部分・やるべきでない部分を明確にすることで製品競争力を高める
前述のとおり製品認証は恐れるべき内容ではなく、日本企業であれば十分に対応可能である。一方で、日本製造業は技術力が高いにも関わらず、グローバル競争において厳しい戦いを強いられている原因の1つに過度な自前主義がある。
例えば、日本メーカは自社内で全てを完結したがる傾向にあり、尚且、リソース(つまり人員)を増やせばなんとかなると思われているところがある。こうした風潮によって日本の製造業は技術力や品質は高いにも関わらず機能安全対応製品における開発では非常に非効率なのが現状である。日本メーカはコア技術と製品の安全性に注力し、専門性の高い内容は専門家に任せてTime to marketを短縮し、製品競争力を高めるべきである。
コア技術は、言うまでもなくこれまで積み重ねてきた、他が真似できない製品競争力の源泉である。それに加え、前述の通り製品の安全性はメーカの責任である。
それ以外の、ツールの信頼性要求やテスト環境構築、Safety通信等は、専門家に任せることが結果的には最も効率が良いケースが多い。例えばSafety通信ではプロトコルが複数ある上に欧米のSafety通信のコンフォーマンステストは日本では出来ない事などもある。
これらの戦略やマネジメントも機能安全対応を製品競争力にする重要な要素である。
自社でやるべきでない部分とは?
機能安全認証において重要なポイントは「専門性が高く、その技術がメーカにとってさほど重要でない部分は自社でやるべきでない。」ということである。本稿では代表的な例として下記3点について各々のパートで業界動向も交えながらできるだけ具体的に解説する。実際の機能安全対応は多岐にわたるが、本稿によって世界観やコツの一部は伝わるはずだ。
- 利用ツール(ツール認定):ユーザー自身が利用ツールの信頼性を保障する必要がある。従来の開発には無い項目であり、意外に大変である。
- テスト環境構築:説明責任と品質を担保できる環境構築が必須である。人力ではなくツールに任せる領域の判断がキーとなる。
- Safety通信:通信プロトコル毎の対応が必要であり難易度が高い。尚且Safetyの場合、Safety用のテストを通す必要があり、自社単独で行うことは非常に困難である。
執筆者紹介 アーキテクト合同会社 代表 高山 哲哉
メーカにて産業用ロボコントローラ(機能安全認証取得)など組込開発の上流~下流、開発及びマネジメントまで幅広く担当。特に国内の機能安全対応が黎明期の頃から、規格適合開発や第三者認証機関との交渉を経験しているため、現在の資産プロセスを生かした現場視点でのアドバイス/交渉が可能な点が強みの会社です。機能安全に関するご相談は、下記までお気軽にお問い合わせ下さい。
お問い合わせ先:info@architect-llc.com
会社URL:http://www.safety-innovation.com